Since the establishment of superhard materials in 1985, and the beginning of undergraduate and postgraduate training, the research work is aimed at international frontier topics in the field of diamonds and related materials, as well as the key issues that restrict the development of diamond tools in China, and domestic and foreign superhard materials manufacturers. Work closely together. He has undertaken the completion of national key scientific and technological attacks, the National Natural Science Foundation, the Huo Yingdong Youth Teacher Fund, the Natural Science Foundation of Hebei Province and the Outstanding Youth Fund Project. The innovative scientific research results obtained by Wang Yanhui as the project leader mainly include: diamond, cubic boron nitride vacuum micro-evaporation plating technology; corundum-coated diamond, cubic boron nitride; diamond, cubic boron nitride low-temperature ultra-pure titanium plating Technology; diamond, cubic boron nitride micropowder titanium plating technology; diamond, cubic boron nitride composite plating alloy technology; diamond and CNT quasi-atomic layer plating technology; nano ceramic bond; non-boiling hydrolysis on diamond and CNT surface deposition oxidation Material technology; nano-diamond electrode materials and electrochemical research.
A number of internationally recognized research results have been obtained in the field of diamonds and related materials, and system theory has been formed in the field of diamond surface plating. Wang Yanhui, Yan Jianbing and their graduate students in Nano Letters, Carbon, Electrochemistry Communications, Nanotechnology, Electrochimica Acta, Surface and Coatings Technology, Applied Surface Science and Diamond & Related Materials More than 70 papers have been published in famous journals, and 50 papers have been included in SCI, and have been cited many times by domestic and foreign papers. Theories and achievements have been quoted by Professor Wang Guangji, Professor Fang Xiaohu, Professor Wang Qinsheng, and Professor Sun Yichao's "Superhard Materials", "New Diamonds and Products" and "Superhard Materials Science and Technology" and many other monographs. Evaluation. Received 5 provincial and ministerial level scientific and technological progress awards.
Many research results have been widely used in industrial applications, such as the “vacuum micro-evaporation plating†technology pioneered at home and abroad, and its professional equipment and raw materials are widely used at home and abroad. Corundum coated diamond and nanoceramic binders are also being used more and more. Since the successful development of nano-ceramic binder in 2006, it has formed a stereotyped grade and has been industrialized in dozens of domestic enterprises. The promotion and application of these results have played an important role in improving product performance, reducing product costs and developing new products.
The innovative scientific research results we have obtained are as follows:
1 Superabrasive surface treatment technology - titanium-plated diamond
1.1 Vacuum micro-evaporation titanium plating technology and its application progress
There is a high interfacial energy between the diamond crystal and most of the metal. There is no interfacial bonding force between the diamond and the binder, and the abrasive grains are easy to fall off during use. Since the diamond concentration in the diamond tool accounts for about 10% of the volume, the diamond particles do not release the diamond particles under the working surface immediately after the diamond particles fall off, so that the diamond particles on the working surface are scarce and do not have the cutting function, resulting in a short life of the diamond tool. low efficiency. Therefore, improving the bonding ability of the metal alloy to diamond and improving the bonding state between the bonding agent and the diamond have been paid attention to by diamond manufacturers at home and abroad.
Because only the strong carbide forming elements such as titanium, chromium, etc. can form a strong bond with the diamond, people initially added some titanium powder and chromium powder to the binder, and hope to improve the bonding state between the binder and the diamond. The results show that the effect is minimal due to the unfavorable factors such as the low contact between the titanium powder and the chromium powder and the diamond, the short sintering time, the insufficient reaction, and the diamond graphitization. The results of numerous scientific and industrial applications over the years have shown that the most effective way to achieve this goal is to plate metals on the diamond surface, such as titanium and chromium. These affinity metal coatings are chemically bonded to the diamond. The metal plating layer is metallurgically bonded to the bonding agent, and the bonding strength is greatly improved.
Before 1991, GE and Debeers had special titanium-plated diamond grades, while China was a blank. In 1991, Wang Yanhui was listed as the subject of the “Superhard Material Plating Technology and Equipment†project. Research projects.
At the beginning of the project development study, we conducted plating tests on strong carbide forming elements such as titanium, chromium, molybdenum, tungsten, vanadium, niobium, tantalum, zirconium and their alloys. It was found that only titanium plating has the lowest temperature and other metals. Plating generally requires a high temperature of 900 ° C or higher, which causes great thermal damage to the diamond after plating. Therefore, titanium-plated diamond is used as a stereotyped product, and under the cooperation and support of China National Machinery Corporation, it has begun industrial application and promotion in Fujian, Guangdong, Shandong, Henan, Hebei and Sichuan. The test tools include stone-sized saw blades, grinding blocks, road saw blades, gang saws and drill bits. The results of the feedback are back. The titanium plating makes the service life of all kinds of diamond tools increase by at least 30%, and the life of tools such as gang saws increases. More than double.
Before we developed the successful vacuum micro-evaporation plating technology, the super-hard material was coated with titanium, etc., using various conventional PVD and CVD methods. These methods cannot be applied in large batches of super-hard abrasives, and between PVD-plated coatings and abrasives. The compound is not formed and the binding force is low; CVD has a high plating temperature and is liable to damage the diamond. In response to these problems, our national key 85 key scientific and technological projects have formed special technologies and equipment for vacuum micro-evaporation plating for industrial coating of granular super-hard abrasives.
In 1994, the results of this project passed the appraisal of the results of the Ministry of Machinery Industry, and the results were completed by Wang Yanhui, Wang Zhiming, and Xingguo. The appraisal conclusion is: vacuum micro-evaporation plating technology and equipment are the first in China and abroad, and are at the international advanced level. Its characteristic is that the amount of plating is large, the cost per carat is less than 0.01 yuan, the plating is uniform, and the plating layer and the diamond have formed a compound bonding layer after plating, which is particularly suitable for large-scale industrial application, and the application effect is remarkable. Since then, internationally renowned superhard materials companies such as Debeers, Rijin, Jiangxin and Italian diamond tool manufacturers have had long-term technical cooperation with us. Debeers commented: "We have always attached importance to plating technology, and we have already formed a lot of coated diamond brands. It seems that Yanshan University's plating technology is ahead of us."
With the increasing use of titanium-plated technology equipment throughout the country, we found that users have difficulty in monitoring the quality of plating materials in the purchase of titanium-plated raw materials, resulting in fluctuations in plating quality. In 2001, a new generation of ultra-pure titanium plating was introduced. Cover technology. The core of the technology is: due to the current level of purity of titanium powder, regardless of its purity grade, it inevitably contains impurities such as magnesium oxide or sodium oxide, these impurities are easier to evaporate than titanium metal, preferentially deposited on the diamond surface, damage the coating quality. Titanium-plated operators will find that after a period of time, the titanium plating equipment will deposit a layer of white deposits in the cooling zone. After analysis, it is a volatile magnesium oxide or sodium oxide. In order to solve this problem, we have carried out high-vacuum high-temperature purification of purchased high-purity titanium. The vacuum purification process parameters are chosen to be much higher than the vacuum degree and temperature of titanium plating, so that volatile impurities are volatilized and eliminated. A new generation of ultra-pure titanium-plated diamond with a bright white coating that further enhances the performance of the tool. In order to protect the legitimate rights and interests of users and avoid the damage of the so-called "vacuum micro-evaporation titanium plating equipment" to the diamond manufacturers, Yanshan University provides users with stable and reliable titanium-plated special raw materials.
The special titanium-plated raw material contains the core technology of “vacuum micro-evaporation plating technology†for more than ten years, achieving the goal of optimal bonding without prejudice to super-hard abrasives, ensuring stable production for all types of users across the country. High quality titanium-plated diamonds play an important role. We have been working on vacuum micro-evaporation plating and incorporating the latest results into titanium-plated special materials.
In recent years, the amount of titanium-plated diamond in the country has increased rapidly. The surface treatment technology represented by titanium-plated diamond has been widely used in the field of super-hard materials. We also apply plating technology to different users and different tool types. Optimized with the binder formulation to achieve the best application results, the tool's performance and price ratio continue to increase.
Using the vacuum micro-evaporation plating technology equipment of Yanshan University and the special titanium-plated raw materials, the titanium-plated diamond produced has a metallic luster appearance; the microstructure is formed by the formation of titanium carbide between the titanium-plated layer and the diamond. The strong combination between the coating and the diamond is combined with the bonding agent to achieve a metallurgical bond between the diamond and the bonding agent, preventing the diamond particles from falling off and improving the utilization of the diamond. At the same time, the plating layer prevents the sintering corrosion of the diamond by harmful metals such as iron in the bonding agent, so that the diamond strength is improved. Therefore, the use of titanium-plated diamond can reduce the amount of diamond, simplify the formulation of the binder, widely use low-cost high-iron formula, reduce product performance fluctuations, and stabilize product quality. It has become an important means for the majority of diamond tool factories to reduce product costs and improve product quality and market competitiveness.
1.2 Effect of Titanium Plating on Life and Sharpness of Diamond Tools
According to the feedback from laboratory research and industrial application for many years, vacuum micro-evaporation titanium has two main functions: to achieve metallurgical bonding between diamond particles and carcass binder, without degranulation, which is equivalent to increasing the diamond concentration; In addition, the titanium coating protects the diamond from corrosion of the diamond during the sintering of the iron-based bond, and the diamond retention strength in the tool increases. Therefore, the service life of the tool can be increased by more than 30%. After using titanium-plated diamond, the user can reduce the diamond usage by 10-20%; the tool cost is greatly reduced and the profit margin is increased.
The way in which diamond particles are destroyed during cutting and grinding can be easily divided into two types: shedding loss and crushing loss. These two ratios are related to the grade of diamond, as shown in Figure 1. As the grade of diamond increases, the amount of crushing decreases and the proportion of shedding increases. Therefore, although titanium plating is effective for all grades of diamonds and tools, the effect of titanium plating is more pronounced with the increase of diamond grade.
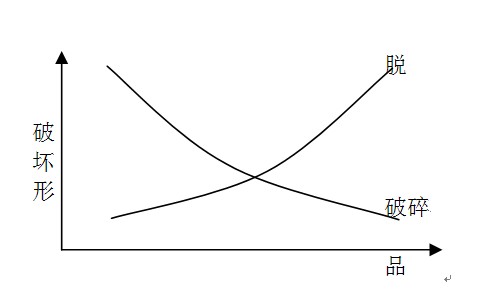
It should be noted that the results of industrial applications show the same concentration of titanium and uncoated diamond. In most applications, titanium-plated diamond greatly improves the service life and efficiency of the tool, but in some applications, the tool has a long life and work efficiency. Low, this is because titanium-plated diamond does not thresh, making the number of diamond particles involved in cutting too much. In this case, reducing the diamond concentration of the tool can both improve tool performance and reduce tool cost. Most manufacturers reduce the amount of diamond used, and tool performance is still higher than uncoated tools.
We use Figure 2 and Figure 3 to analyze the above phenomenon.
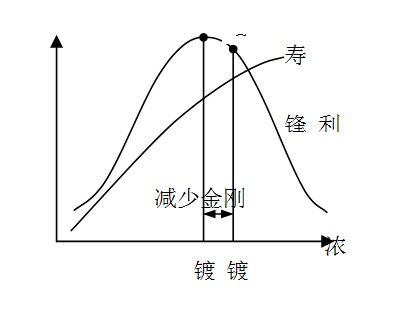
In diamond tools, the concentration of diamond has a large effect on the life and sharpness of the tool, as shown in Figure 2. Starting from a very low concentration, as the diamond increases, the tool's service life and sharpness increase. When the optimum concentration is reached (the tool's sharpness is highest), continuing to increase the diamond will reduce the sharpness. In general, most tool factories have undergone repeated industrial test adjustments to make the diamond concentration at the optimum concentration (ie, the sharpness is best at point A of Figure 2), and there are also tool factories that have lower diamond concentrations in order to reduce costs. , at the point B concentration in Figure 3. For diamond tools that are already at the optimum concentration (ie, point A in Figure 2), titanium plating results in a significant reduction in diamond shedding, which is equivalent to a significant increase in diamond concentration, ie titanium plating causes the diamond concentration to move from A of Figure 2. At point C. Reflected in the use of tools, titanium plating has improved tool life, but the sharpness has decreased. At this time, the amount of diamond to be reduced is reduced. The theoretical reduction is the difference between the two points A and C in Figure 2. According to the results of industrial application, the amount of diamond is generally reduced by 10-20%, and the tool can be maintained. Best life and sharpness.
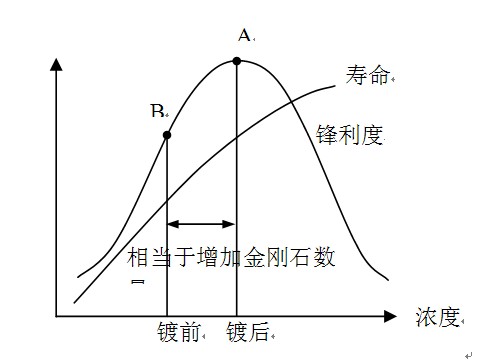
For diamond tools with lower diamond concentration, at the point B concentration in Figure 3, the titanium-plated diamond does not fall off, so that the diamond concentration in the tool increases, and the diamond concentration moves from B in Figure 3 to point A. In this case, the practical application The effect is that the titanium plating makes the life and sharpness of the diamond tool increase at the same time, and the amount of diamond can be reduced without reducing or appropriate amount.
1.3 Effect of titanium-plated diamond on binder
The performance of the diamond tool after titanium plating is less sensitive to the performance of the bond. When there is no titanium plating, the bonding agent must bear two functions. Firstly, the sintered body is formed with diamond to form a tool with certain strength and wear resistance. Secondly, the bonding agent must be mechanically embedded in the diamond to prevent falling off, so the bonding agent is hard. Blunt, soft, short life, extremely difficult to adjust and stabilize quality. After the titanium-plated diamond is used, the diamond and the bonding agent are strongly welded together, and the loss of diamond during high-temperature sintering is avoided. As long as the binder is well sintered and the quality is stable, a large amount of low-cost raw materials can be used.
Titanium-plated diamonds have reduced requirements for binders due to strong bonding, simplifying the requirements for binder formulations, eliminating or substantially reducing the amount of expensive non-ferrous metals, enabling the widespread use of high-iron (75%) binders, such as the current market adoption. 95% copper-clad iron powder, plus 5% tin powder, is a simple formula to make low-cost diamond saw blades.
In addition, titanium-plated diamond reduces the influence of raw material, process and mold fluctuation on tool performance, which is conducive to ensuring product quality and stability, and greatly improving the market competitiveness of super-hard tool products.
1.4 Economic Benefit Analysis of Titanium-plated Diamond
According to the results of large-scale industrial application and the above analysis over the years, the economic benefits obtained by using titanium-coated diamond manufacturing tools are as follows:
1) Low cost, plating cost per carat <0.01 yuan.
2) The use of titanium-plated diamond can reduce the amount of diamond by 10-20%, and can appropriately increase the amount of fine-grained diamond at a low price.
3) Titanium-plated diamond simplifies the requirements of the binder formulation, cancels or greatly reduces the amount of expensive non-ferrous metals, and achieves the wide application of high-iron (75%) binder.
4) Stabilize product quality. Titanium-plated diamond reduces the influence of raw material, process and mold fluctuation on tool performance, which is beneficial to ensure product quality and stability, and greatly enhances the market competitiveness of super-hard tool products.
2. Micro-powder special plating technology and application
On the basis of the successful development and industrial application of vacuum micro-evaporation plating technology, Wang Yanhui was responsible for completing the special coating technology for micro-powder in 1997, and realized the industrialized titanium plating production of super-hard material micro-powder for the first time at home and abroad. This technology is suitable for micro-powder and 200-mesh fine super-abrasive plating. The process is simple and controllable, and the cost is low. The micro-powder plating technology satisfactorily solves a series of industrial technical problems such as uneven plating and adhesion of fine powder, and can realize large-scale industrial production.
Ordinary vacuum-plated titanium, the finest to 325 mesh, and subsequent processing is very difficult as the particle size becomes fine, can not be coated with micro-powder diamond, due to the ultra-fine size of the diamond micropowder, large surface area, easy to splash, difficult to settle and separate. Therefore, various types of plating methods and various types of plating are difficult for the micro-powder plating operation. Electroless plating, electroplating and other solutions are plated with nickel, copper, etc. The huge surface area makes the electroless plating solution unstable. The fine powder floats in the plating solution and cannot be thickened by barrel plating. The micro-powder plating is easy to form adhesion, and the plating solution and the fine powder are difficult to separate. A series of rinsing processes from activation-sensitization-electroless plating-electroplating are very complicated, and the fine powder is easily lost in a large amount. Therefore, it is almost impossible to produce a qualified product by the solution plating method, and even if it is barely plated, there is a high cost and a rejection rate. High, uneven plating, leakage plating, severe adhesion and other problems.
Titanium-plated superhard material micropowder applicable tool products are as follows:
1. Diamond refining sheets that have been widely used in the field of optical glass processing.
2. Diamond polishing tools in the field of stone and vitrified ceramic tile polishing and polishing.
3. Titanium-plated diamond powder is used in the manufacture of wire saws to increase the speed of sanding and the speed of thickening. The life and sharpness of the diamond wire saw are greatly improved. 4. Metal and ceramic bond diamond fine grinding wheels for sharpening various types of superhard polycrystalline cutting tools.
5. Titanium-plated superhard material micropowder is used to manufacture super-hard polycrystalline products with medium combination.
In addition to completing the titanium-plated diamond micro-powder technology and equipment, Wang Yanhui also completed the National Natural Science Foundation of China: research on nano-diamond plating technology, and obtained innovative technologies for titanium and silicon plating of quasi-atomic layers on micro-nano-sized diamond surfaces; Non-boiling hydrolyzed oxide deposition technique. As a result, plated diamonds range in size from nanometers to nanometers, and coatings range from metals to non-metals and oxides, greatly expanding and enriching the coating of superhard materials.
3. Composite Ti-Ni technology and its application
After the diamond is vacuum-deposited by titanium, since the conductive metal layer is already available, the electroless nickel plating or electroplating nickel can be directly used (without prior treatment such as sensitization and activation) to form a composite plating layer. Nickel coated with titanium by vacuum micro-evaporation can also be directly electroplated with nickel. This composite plating process eliminates many cumbersome processes such as sensitization, activation, electroless plating, etc., low cost, large batch size, short cycle, good quality, no leakage. plating. Suitable for large-scale industrial production of composite coated diamond, is a new generation of composite plating process and technology with great cost and quality competitiveness.
It must be pointed out that the structure and properties of the composite diamond-plated diamond formed by vacuum-plating titanium and then further nickel plating are completely different from ordinary nickel-plated diamond. Composite diamond plating First, titanium and diamond have formed titanium carbide, and the nickel plating layer is easily brazed to the substrate.
The application of composite titanium-nickel alloy diamond is as follows:
1) Composite Titanium Nickel Alloy Diamond for Metal Sintering Bonding Tools
The feedback results of the industrial application show that the composite titanium-plated nickel diamond can further improve the use effect of the titanium-plated diamond, and the service life and sharpness of the titanium-plated diamond are increased by 10%.
2) Composite Titanium Nickel Alloy Diamond for Brazing Diamond Tools
The composite diamond plating and the brazing material are well infiltrated, and the combination is firm, and the grinding wheel is strongly polished and does not fall off.
3) New process for nickel plating of low grade superabrasive for resin bonding
4 corundum coated superhard abrasives and applications
As early as the 1960s, copper-plated and nickel-plated diamonds were used to make resin grinding wheels. Due to the high price of diamonds at the time, copper-plated and nickel-plated diamonds improved the service life of grinding wheels and gained widespread application. The development of superhard materials to date, the cost of nickel plating is close to the cost of diamond abrasives, and the thick nickel coating hinders grinding and reduces sharpness.
In order to solve this problem, Wang Yanhui developed a superabrasive abrasive coated with corundum in 2001. Using hard and brittle corundum or silicon carbide as the coating, the coating is uneven and has a "thorn shape", which is firmly combined with diamond and cubic boron nitride. In the resin-based grinding wheel, the holding force of the super-hard abrasive and the substrate can be improved and prevented. Early shedding of abrasive grains. In addition, the brittle corundum coating does not hinder the grinding process, thus improving the service life and sharpness of the grinding wheel, which provides a proprietary technology for solving the long-standing contradiction between the service life and the sharpness of the grinding wheel. China National Mills Co., Ltd. used corundum-coated diamond-made resin grinding wheels to export to the United States, replacing the traditional nickel-plated diamonds, which has been approved by users. At the same time, the results of domestic manufacturers show that the diamond-coated resin grinding wheels are used to improve the life. And sharpness, to achieve the performance of similar products in Taiwan and Japan. Jiangxin Company uses our technology to produce corundum-coated diamond abrasives, which has formed a special grade and has been applied internationally. Its good and stable application effect has been widely praised at home and abroad.
The corundum-treated diamond and the cubic boron nitride have a weight gain rate of generally 50% by weight, which can be arbitrarily adjusted as required. The single-particle compressive strength after coating can be increased by 12 to 65%. The results of industrial application show that the super-hard abrasive treated by this process not only has the advantages of nickel-plated and copper-plated super-hard abrasive, but also overcomes the disadvantages of high plating cost and dullness of the tool, making the resin bond superhard tool The service life is increased by 20%, the processing efficiency is increased by 30-35%, and the performance price ratio of the tool is greatly improved. The most important characteristic is that the coated abrasive has good self-sharpness and significantly improves the cutting efficiency.
The surface of the diamond and cubic boron nitride after the corundum coating treatment showed a granule full of small thorns. The surface morphology of the diamond after the corundum coating treatment is shown in Fig. 4.
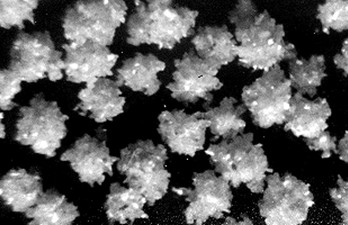
In 2001, the corundum-coated super-hard abrasive passed the identification of scientific and technological achievements in Hebei Province, which was the first in China and abroad and was at the international advanced level. In 2003, he won the third prize of scientific and technological progress in Hebei Province, and completed the man-made: Wang Yanhui, Wang Zhiming, and Qi Jianbing.
5 nano ceramic bond
Due to the high sintering temperature and low strength of traditional ceramic bond, the true low-melting and high-strength ceramic bond is the key to the manufacture of internationally advanced diamond and CBN ceramic abrasive tools. In order to solve the problem of low temperature and high strength of ceramic bond, we have carried out long-term exploration with many domestic research groups, including the optimization of various oxides. The theory, distribution ratio and process of glass-ceramics are used for ceramic bond. Although the development of the company has made some progress, it has been restricted by the complicated process and many factors that cause the performance to be unstable. On the basis of a one-year study of nano-low-melting high-strength ceramics at Imperial College London in 2005-2006, Wang Yanhui used nano-materials as a binder to significantly reduce the sintering temperature and greatly improve the strength, toughness and wear resistance of the products. The experimental results are stable and reproducible, and have been successfully applied in industrial applications.
Its main performance characteristics are: 1. Low sintering temperature, ceramic bond sintering temperature for diamond abrasives 700--850 °C, ceramic bond sintering temperature for CBN abrasives 800--900 °C; bond bending resistance The strength is higher than 100 MPa. 2. Low density, 2.68, only 1/3 of metal bond, with cost advantage. 3. Nano-ceramic binder and diamond and CBN super-hard abrasive have good wettability and strong bonding force, do not react with super-hard abrasive during sintering, do not corrode and damage super-hard abrasive, uniform distribution of abrasive and binder, good infiltration . The product has been successfully used for grinding ceramic diamond micro-powder wheels of PCD composite sheets, ceramic CBN grinding wheels for grinding rotor grooves, various CBN ceramic bond grinding heads, and CBN and diamond whetstones. Nano-ceramic binders are suitable for a wide range of particle sizes, especially for the production of fine-grained, micronized, fine grinding tools and sharpening tools, with the incomparable advantages of common ceramic binders.
The nano-ceramic binder is divided into two categories of dense and uniform pore type; according to different application requirements, after sintering, a non-porous dense product and a uniformly distributed circular pore can be obtained. And according to the user's requirements, the porosity can be adjusted in a wide range, suitable for the development of different user tool types. Currently stereotyped products: nano-low temperature N680; nano high-strength N730; nano-wear N780; nanoporous N830.
At present, there is an increasing demand for ceramic bond superhard tools. Domestic superhard tool manufacturers are actively developing ceramic bond diamonds and CBN tools, and have successfully replaced expensive import tools in some types of tools. However, domestic superhard tool manufacturers make their own and melt the vitrified ceramic binder, which has complicated procedures and many factors affecting the performance of the binder, resulting in poor product stability. The nano ceramic bond developed by us can be used directly as long as there is a certain tool manufacturing base, the process and process are simplified, the investment is small, and it is easy to launch, which is conducive to the development of various tools suitable for the user's own market characteristics.
F Ground Screw, which means Ground Screw with Flange and it is called "Solar Ground Screws ". Plenty of F series Ground Screws are exported to global customers of Ground Screw from all world. Flange of ground screw can be classified as round flange, square flange, hexagon flange, triangle flange, A flange, Helical flange, U flange, A flange and so on. We will do different flanges for you as your needs. You can supply us some drawings of ground screw and then we will do molds for you. Generally, we will protect your rights of drawings and can not disclose the information of drawings you supplied. The main application of ground screws is used to solar mounting systems, ground mounting systems, solar panel structures, wooden house, farming installing, buildings supporting and prefab houses.
F Ground Screw
F Ground Screw, Ground Screw Piles, Ground Screw with Flange, Solar Ground Screws, Free Sample Ground Screws, Foundation Ground Screw, Galvanized Ground Screws
Hebei Honde Industrial Trade Imp&Exp Co., Ltd. , https://www.groundscrewpile.com