I. Trouble during commissioning This type of fault occurs when the electromagnetic flowmeter is initially installed and debugged, but once it is improved, it will not appear again under the same conditions. Common failures during the commissioning period mainly include three reasons: improper installation, environmental interference, and fluid characteristics.
1. The piping system and installation are usually faults caused by incorrect installation position of the electromagnetic flow sensor. For example, the flow sensor is installed at the high point of the pipe network which is easy to accumulate the retained gas; after the flow sensor, there is no back pressure, and the liquid is straight. The human atmosphere forms a non-full tube in the measuring tube; it is installed on a vertical pipe that flows from the top to the bottom, and may be evacuated.
2, the environmental aspects are mainly pipeline stray current interference, space electromagnetic wave interference, large motor magnetic field interference. Pipe stray current interference usually takes good separate grounding protection to obtain satisfactory measurement, but if there is strong stray current in the pipeline (such as electrolysis workshop piping), it may not be overcome, and the flow sensor and pipeline must be taken (see below) Case 12). Space electromagnetic interference - usually transmitted through a signal cable, usually protected by a single layer or multiple layers of shielding, but it has also been overcome by shielding protection (see Case 10).
3, the fluid aspect of the liquid contains evenly distributed fine bubbles usually does not affect the normal measurement, only the measured volume flow is the sum of the liquid and the gas; the increase of the bubble will cause the output signal to fluctuate, if the bubble is large enough to flow through the electrode to cover the entire electrode surface To make the electrode signal loop momentarily open, the output signal will produce more fluctuations. Low-frequency (50/16 Hz-50/6 Hz) rectangular wave excitation electromagnetic flowmeter will produce slurry noise when the liquid contains more than a certain amount of solids, and the output signal will also fluctuate to some extent. When two or more liquids are used in the pipeline mixing process, if the conductivity of the two liquids (or the potential between the electrodes) is different, the flow sensor is measured before the mixing is not uniform, and the output signal also fluctuates. The electrode material and the measured medium are poorly matched, and chemical effects such as passivation or oxidation, formation of an insulating film on the surface of the electrode, and electrochemical and polarization phenomena may hinder normal measurement.
Second, the fault during the initial period of operation and the normal operation after a period of time, the common faults are: the inner layer of the flow sensor, the lightning strike, the environmental conditions change.
1. The adhesion layer on the inner wall Because the electromagnetic flowmeter measures the suspended solid phase or the dirty body much more than other flow meters, the probability of failure of the inner wall adhesion layer is relatively high. If the conductivity of the adhesion layer is close to the liquid conductivity, the meter can output the signal normally, but only change the flow area to form a hidden fault of the measurement error; if it is a high conductivity adhesion layer, the electromotive force between the electrodes will be short-circuited; if it is an insulating adhesion layer The surface of the electrode is insulated to disconnect the measuring circuit. The latter two phenomena will make the meter inoperable.
2. Lightning lightning strikes induce instantaneous high voltage and surge current in the line, and entering the meter will damage the meter. There are three ways to introduce the lightning damage meter: the power line, the flow signal line between the sensor spoon converter and the excitation line. However, from the analysis of damaged components in lightning faults, the induced high voltage and surge currents that cause faults are mostly introduced from the control room power line, and the other two approaches are less. It was also learned from the scene of the lightning strike that not only the electromagnetic flowmeter was faulty, but also other instrumentation in the control room often had lightning strikes at the same time. Therefore, the user must know the importance of setting up the lightning protection facilities of the control room instrument power cord.
3. The main reason for the change of environmental conditions is the same as the fault environment in the commissioning period of the previous section, except that the interference source does not appear during the commissioning period and then intervenes during the operation. For example, an electromagnetic flowmeter with unsatisfactory grounding protection has normal operation due to no interference source during commissioning. However, new interference sources (such as pipelines near the measuring point or pipeline welding) interfere with the normal operation of the instrument during operation. , the output signal fluctuates greatly.
Orifice flowmeter http://
Radar level gauge http://
Input type liquid level transmitter http://://news.chinawj.com.cn
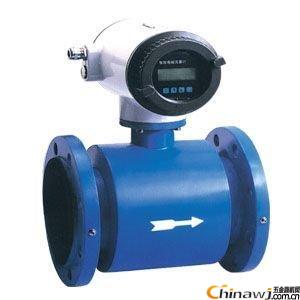
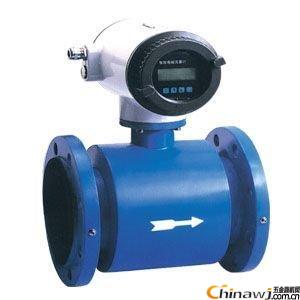
HHCMS-200 carbon molecular sieves
CMS-200 is a new kind of non-polar adsorbent specially designed for extracting nitrogen-rich gas from air. It is suitable for separating nitrogen from air. It has a high adsorption capacity for oxygen and can separate nitrogen from air.
The most notable feature of the Carbon Molecular Sieve is its high gas-producing efficiency, especially the preparation of nitrogen with a purity of less than 99.5%.
It is widely used in large air nitrogen making equipment.
Project parameters
The diameter of:1.0-1.3 1.3-1.5
Packing density:≥660kg/m³
The intensity of particle:≥95
Compressive strength abrasion:≤1%
The moisture content:≤0.5%
Standard packing:20Kg/barrel. 40Kg/barrel. 130Kg/barrel
The adsorption time of test condition was 58s with an average pressure of 1-2s
Adsorption pressure |
Nitrogen purity (%) |
Yield (Nm3/ h.t.) |
Nitrogen recovery rate |
0.8MPa |
99.9 |
120 |
30 |
99.5 |
200 |
37 |
|
99 |
250 |
41 |
|
98 |
310 |
45 |
|
97 |
370 |
47 |
|
96 |
420 |
50 |
|
95 |
490 |
55 |
|
0.6MPa |
99.9 |
95 |
31 |
99.5 |
160 |
38 |
|
99 |
200 |
43 |
|
98 |
245 |
46 |
|
97 |
300 |
49 |
|
96 |
335 |
51 |
|
95 |
390 |
56 |
Pay attention to
1. The nitrogen production equipment can reduce the adsorption temperature to better show its excellent nitrogen production performance under conditions;
2. Pay attention to low temperature drying and seal preservation during storage;
Molecular Sieves Hhcms-200,Molecular Sieve Regeneration,Activate Molecular Sieves,Psa-Carbon Molecular Sieves
Zhejiang Changxing Haihua Chemical Co.,Ltd. , https://www.zjcxhhcms.com