Residential building exterior wall bookmark0 □ Beijing General Housing Real Estate Development Co., Ltd. Ni Shijie The Ministry of Public Security residential building project has a total construction area of ​​152,314 m2, underground construction area of ​​47,061 m2 and above-ground building area of ​​105,253 m2. There are five towers on the ground and the structure is fully cast concrete shears. Force wall structure. External insulation of residential building uses extruded polystyrene board plug-in large mold built-in cast-in-place concrete external wall insulation system, insulation board installation area of ​​more than 50,000 square meters.
The insulation of five towers adopts exterior wall insulation. The insulation system adopts the method of fixing the extruded polystyrene board using the 8J2 drawing board with large plug-in plug connectors. However, in the 88J2 drawing set, it is only a design drawing. At present, there are no engineering examples and corresponding industry and local technical standards, and there is no corresponding information on the material requirements and construction technology. Therefore, there is a great technical difficulty in construction. In view of this situation, it is necessary to fully demonstrate the key factors such as safety, heat preservation and durability of the practice through theoretical calculations and field tests, and propose corresponding technical requirements.
Technical points Before the construction, the adhesive strength between extruded board and cast-in-place concrete was tested on site. The average pull strength between extruded board and cast-in-place concrete was 0.011Mpa (11KN/m2). The pull-out force of the plug and concrete structure is 3.5KN/piece. According to the standard layer, the width of each extruded sheet is about 0.6m, and the height is about 2.8m. The plug plug is used in 19-20 calculations. The number of bolts is about 11.1, which is equivalent to 38.8KN/m2. Therefore, the total value of the maximum wind pressure at a height of 100m above the urban suburbs (surface roughness class B) in Beijing is 3.58. Therefore, in theory, the extruded plates and structures are The safety coefficient of the wind pressure resistance between the wall can reach 13.9.The connection between the screed mortar and the extruded plate depends mainly on the cohesive force of the two.In order to ensure the better adhesion of the extruded plate and the screed mortar, in the extrusion The brushing interface agent on board is detected by the National Building Materials Quality Supervision and Inspection Center up to 0.24Mpa, far exceeding the average pullout strength of the extruded board and the cast-in-place concrete wall, which is enough to resist the effect of wind load.
From the above analysis, the connection between the insulation system and the wall is safe and reliable. At the same time, in actual construction, the tensile strength between the extruded plate and the cast-in-place concrete should be taken into consideration much smaller than that specified in the general external insulation. MPa, the tensile force is mainly borne by the steel-plastic composite plug, and the strength of the extruded plate itself is also less than the strength of the steel-plastic composite plug bolt. In order to ensure the anchoring effect of the plug bolt, the protective layer mortar needs to In addition to sufficient bonding strength with the extruded board, the reinforcing mesh must be firmly connected with the plug bolt by means of construction measures, and the gravitational force of the mortar is transferred to the structural wall body through it. The flatness and perpendicularity of the surface require that the average thickness of the plastering mortar is about 2cm. Considering that the coating finish has higher requirements for crack prevention, a layer of glass must be added to meet the requirements for leveling the polymer mortar. The thin plastered flexible polymer mortar compounded by the fiber mesh cloth, plus the weight of the real stone paint, is about 45Kg/m2. The insertion force test of the insertion force can be concluded that the load on the single insertion crucible at this time is 4Kg. The crucible tends to stabilize after being loaded for 1 minute to 24 hours, and its deformation amount is about 0.44 mm, so it can fully meet the safety requirements.
The project uses a 60mm thick extruded plate, and its thermal conductivity is 0.028WAm, K). After being compounded with 200mm thick concrete, the main body heat transfer coefficient (the thickness of the mortar is as follows, the external wall thermal insulation performance of the project meets Beijing 65% energy saving requirement.
The entire external thermal insulation project is a relatively complex system. It is not enough to measure the durability of mortar and wire mesh alone. It also needs to be verified through large-scale weatherability tests. After the plastering mortar and wire mesh have passed the test of 80 hot rains and 5 cycles of freeze-thaw cycles and are still able to meet the relevant standards, their durability can be considered as reliable.
In order to ensure the durability of the insulation system, weather resistance tests were carried out on the KE polymer mortar, which was specially used for external insulation development and production of the KE polymer mortar after the first welding, and the steel wire mesh and the extruded board. After the weathering test, no cracking or hollowing occurred in the trowel mortar, and both the pull strength and the impact strength met the requirements.
The main points of construction are polystyrene extruded foam insulation board with a model specification of 60mm. The material was sampled at the site and tested for its compressive strength, thermal resistance, thermal conductivity, dimensional stability and combustion properties. All meet the requirements of GB/T10801.2-2002 "Insulation Extruded Polystyrene Foam (XPS)".
The KE-2 multi-purpose building glue provided by the Beijing Science and Technology Development Center has been tested by the China Building Materials Institute. The tensile bonding strength of the extruded board exceeds that of the polystyrene board (breakage of the extruded board during inspection).
The use of steel-plastic composite plugs, model number TBS-A-140. The material was sampled and submitted to the site to test the tensile strength of a single anchor bolt, the test result was 3.5KN. Polymer cement dry mortar, KE dry mix, Multi-functional construction adhesive (KE, KE-3) uses polymer cement dry mortar, KE dry mix, multi-functional construction adhesive (KE, KE-3), after on-site commissioned inspection, sent dry mortar, KE dry blend , KE-3 glue, KE glue, test results meet the requirements.
Galvanized steel wire mesh, alkali-resistant glass fiber mesh cloth using welded hot-dip galvanized steel wire mesh, its specifications model fiber mesh cloth, specifications and models for the 5X5, 160g/m2. After on-site re-inspection, test results meet the requirements.
2. Installation process and quality control of extruded board Installation of extruded board A wall template A concrete pouring A demoulding template Quality control of the installation process: (1) Acceptance of the extruded plate (plate acceptance, interface Qi Qingqing J acceptance) Materials approached by Material group is responsible for acceptance, product specifications, type, quantity, density, certificate, test report, instruction manual, technical disclosure, etc. meet the requirements, complete data. After the material enters the site, the tester is responsible for the sample test and acceptance before it can be used.
Before the construction of technical demonstrations and model demonstrations, a special construction plan was prepared. The director’s organization organized the submission of the special plans. Each building number was managed by the construction manager of Building No. No., and each building number was constructed at the first floor. The construction model will be organized and implemented in large areas after acceptance by the technical and quality departments.
After the wall bars are bundled and qualified by the supervision and acceptance, the heat insulation plate and the steel frame are connected firmly with plug bolts. Vertical lines are placed at the yin and yang corners of the external walls of the building. . When the seam width exceeds 2mm, it shall be filled with a piece of polyphenylene plate with a corresponding thickness. The seam height difference shall not exceed 1.5mm, otherwise it shall be smoothed and polished with sandpaper.
When used for face tile finishes, the distance between the A-type steel-plastic compound plugs is 300×350mm. When installing the insulation board, the cement mortar pad should be tied at the insert bolt position on the inner side of the insulation board at a spacing of 600×700mm.
First install the insulation board at the corner of the yin and yang and then install the insulation board between the corner boards.
Before installing the insulation board, the polystyrene board styrofoam should be evenly coated at the notch of the insulation board, and the vertical joints of the insulation board should be affixed with each other. The polyphenylene board quilt is processed by the processing plant and transported to the site.
After mold clamping control and mold closing acceptance of polystyrene board acceptance of external insulation board allows the installation of templates. Before installing the external wall formwork, positioning measures (large form top formwork bars) must be taken on the outside of the thermal insulation plate to ensure the position of the large formwork is accurate. At the same time, the template is prevented from pressing against the insulation board, the template placed on the triangle platform is in place, and the bolts are tightened and tightened through the wall. The connection must be tight and firm to prevent the occurrence of the wrong stage and the phenomenon of slurry leakage.
The slump of cast-in-place concrete shall be 180mm. When the concrete is poured, the mouth of the insulation board must be protected. Before the pouring of the pouring concrete, a protective cap shall be put on the upper part of the notch of the insulation board. The shape of the protection cap is *n* type. The width is the thickness of the insulation board + the thickness of the stencil, made of galvanized iron sheet. When using, hold the insulation board together with the large board. When the rings are encountered, the rings should be placed in the openings on the upper side of the protective cap.
When tying the top steel bar, the external wall thermal insulation board must also be protected to prevent damage to the thermal insulation plate.
The height of each layer is less than 500, and the material should be evenly distributed when the material is removed. The vibration distance of vibrating rod should be less than 500mm. The duration of each vibrating point should be floating slurry and no longer sink to the surface. It is forbidden to use vibration. Stick close to the insulation board.
When the concrete is poured at the entrance of the cavern, it shall be cut along both sides of the cavern at the same time so that the pouring height on both sides should be kept approximately the same.
Under normal temperature conditions, the strength of the wall concrete shall not be lower than 1Mpa. In the winter construction, the wall can be decomposed after the concrete is not lower than 4Mpa and meets the temperature requirements. When the template is removed, the compressive strength of the curing specimen with the same conditions shall be taken as the criterion. .
Dismantling the template of the outer wall state first, then removing the inner wall of the outer wall and must timely repair the concrete corners and board surface slurry.
After the wall casing is removed, holes should be used to dry and harden the mortar. The holes of the insulation board must be blocked with thermal insulation material and penetrate the wall. When the template is lifted, the thermal insulation board will not be impacted and the thermal insulation damage will occur. After the first layer of positive angle is released from the mold, it is timely protected with a bamboo plywood to prevent the edges and corners from being damaged. The bottom of the pylons and the contact surface of the wall are filled with pad to prevent the pylons from squeezing the insulation board.
3. Main processes and quality control of finish construction Polymer plastering and surface layer construction process Brushing interface agent One base layer treatment Hanging wire mesh and fixing a leveling layer Polymer mortar One layer of flexible polymer mortar One layer of paste, pressure net Gebu touched a layer of flexible polymer mortar, repaired and accepted a real stone paint spraying polymer plaster and surface layer construction process control of the use of materials and finished products, after passing the quality inspection and acceptance, its variety, specifications, performance all in line with the design And related standards. On-site sampling retest interface agent, galvanized steel wire mesh, polymer mortar, glass fiber mesh cloth, flexible polymer mortar.
The process and the demonstration of the process and the demonstration of the concrete exterior wall plastering program, clear process methods, carefully organize the bottom, and on the 1st floor as a construction model.
Leveling layer process control and acceptance After the grassroots cleaning, apply KE*2 glue on the surface of the extruded board as an interface agent. The brushing surface is even and there is no omission. Then the steel mesh is laid. The surface polymer mortar plastering process is performed after the steel wire mesh is laid. The grassroots processing and laying network are all subject to sub-item acceptance. After passing the qualification, the next process will be carried out.
The thickness of the mortar under the steel wire mesh is 8mm, and the thickness of the wire mesh mortar is about 7mm. The surface is smooth and the wire mesh is not exposed. The allowable deviation of the surface roughness of the plastering layer is 4mm, and the allowable deviation of the verticality of the facade is 5mm. After acceptance, it basically meets the requirements.
(4) Flexible polymer mortar process control, acceptance control leveling After 2 to 3 days after the completion of the construction of the polymer mortar, a thin plastering flexible polymer mortar plastering process was performed. The total thickness of the thin plastering flexible polymer mortar was 3 mm. The surface of the polymer mortar was plastered with a thickness of 2 to 3 mm. The pressure was applied to the grid cloth: The grid cloth was stretched and then put on the bottom screed. The grout was pressed into the mortar with a trowel from the middle to the periphery. The surface layer is flat and compact, and the grid cloth has no wrinkles. The grid cloth is stuck on the surface of the mortar and exposed to the bottom mortar. Single-mesh length 5mX5m. Lapping horizontal 100mm, longitudinal 80mm. Wiping layer mortar in the bottom surface of the mortar before setting a smear mortar cover, thickness of 1-2mm, to cover only the grid cloth, micro See the grid layout. Surface mortar should not be constantly rubbing, so as to avoid the formation of empty drums.
After the plastering layer has passed the experience, it is allowed to proceed to the next process. The professional construction unit organizes the construction in strict accordance with the special construction plan and strictly controls the construction quality in accordance with relevant regulations.
Testing and Acceptance Each batch of approach materials for this project is provided with product certification and inspection report of the manufacturer. Sampling tests and retests are performed on site according to requirements, including 2 times for extrusion board, 2 times for insertion, 1 interface agent, and steel wire mesh. Alkali resistant fiberglass cloth 8 times, plastering mortar 11 times, retest test reports meet the relevant standards.
The principle of acceptance of sub-items for external insulation shall be checked and accepted according to one inspection lot per floor for each inspection. 27 batches of 1st floor, 23 batches of 2nd floor, 27 batches of 3rd floor, 23 batches of 4th floor, 23 batches of 5th floor, a total of 123 inspection batches, inspection items All are in compliance with the relevant regulatory requirements, and the acceptance of the external thermal insulation sub-projects is satisfactory. ST
Swimming Kickboard is an ideal tool for swimming learning and exercise. The kickboard is designed to help children learn to swim and provide confidence in water.
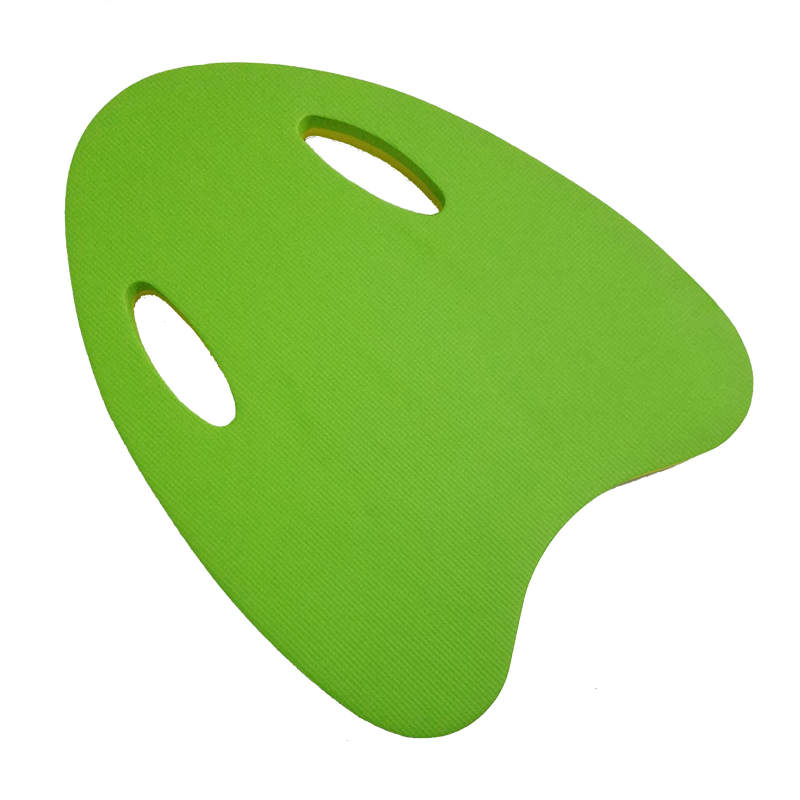
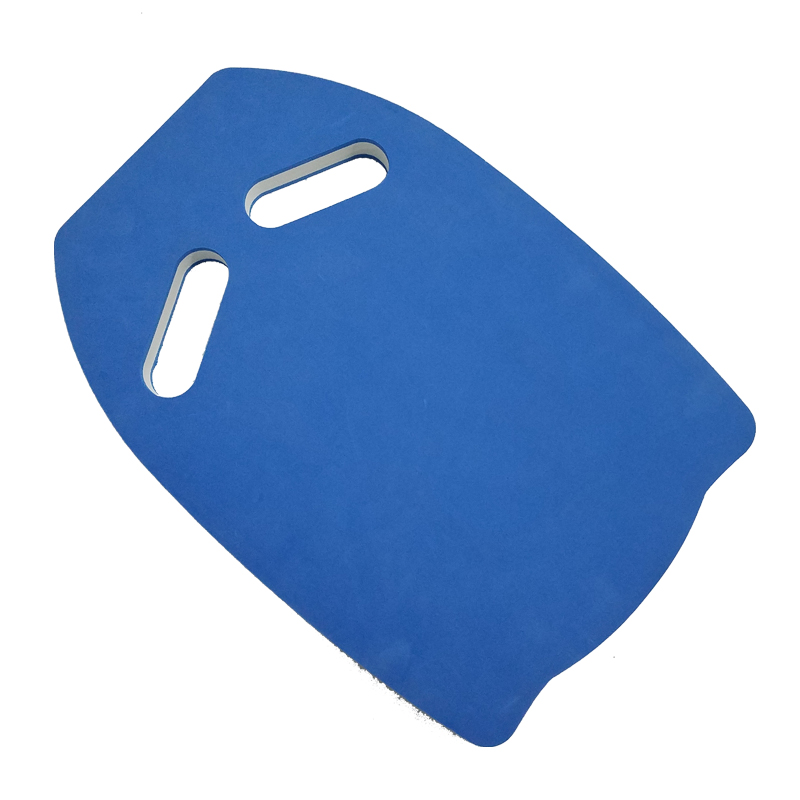
We can make customers' logo on our existed design kickboard, or make a new design of kickboard based on the design.
Please note that the Swimming Board is not an life saving device, children can use this product only under the supervision of an adult.
Swimming Kickboard
Swimming Kickboard,Eva Kickboard,Pool Kickboard,Swimming Board,Pool Kick Board,Swimming Float Board
Huizhou Melors Plastic Products Factory , https://www.melorsfoam.com