**Abstract**
Large residual capacity, heavy load, and automatic belt grinding are common in various industrial applications. Examples include the grinding of automobile engine connecting rod ends, boiler pipeline polishing, and the surface treatment of nuclear power high-pressure vessels. These operations require robust, efficient, and highly automated equipment to meet strict precision and productivity standards.
**Key Features of the Grinding Equipment:**
1. Due to the large grinding allowance (typically 1mm or more), the machines are designed with multiple stations, combining abrasive belt polishing with grinding wheel operations, or allowing for quick switching between the two.
2. The workpieces involved are often large and heavy, requiring the grinding equipment to be similarly sized and built for durability.
3. The equipment operates for long periods in harsh environments, demanding high reliability and maintenance efficiency.
4. Automation is a core component, ensuring consistent quality and reducing labor intensity.
**1. High-Efficiency Belt Grinding for Automobile Engine Connecting Rod Ends**
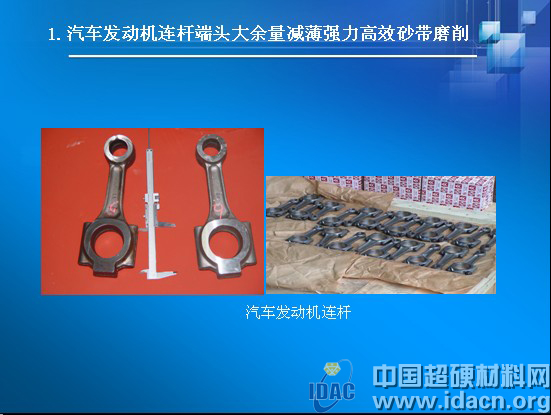
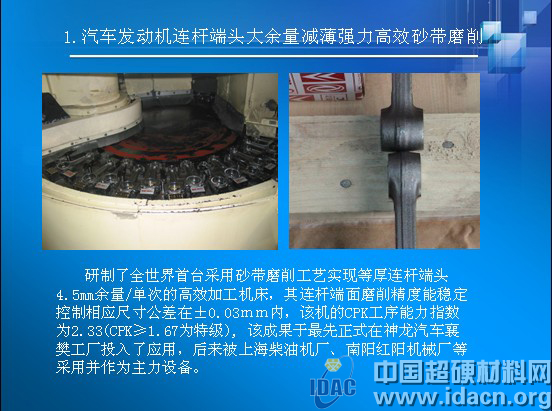
The world’s first high-efficiency machine using abrasive belt grinding was developed to process connecting rod ends with a 4.5mm margin and constant thickness. It achieves a stable grinding accuracy of ±0.03mm, with a CPK value of 2.33—far exceeding the industry standard of 1.67. This technology was first implemented at the Shenlong Automobile Xiangfan factory and later adopted by major manufacturers such as Shanghai Diesel Engine Factory and Nanyang Hongyang Machinery Factory, significantly improving production efficiency and quality.
**2. Abrasive Belt Grinding for Boiler Pipelines**
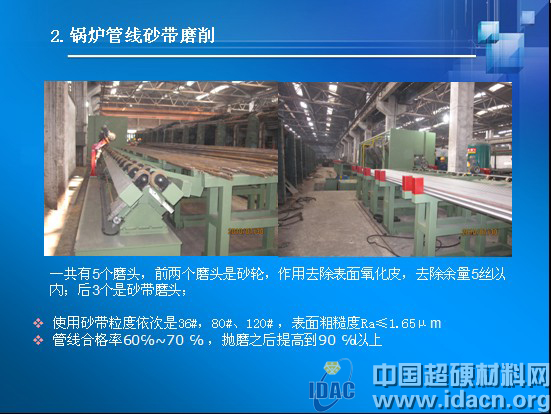
This system uses five grinding heads, with the first two being grinding wheels for removing oxide scale and the remaining three being abrasive belt units. The belts have grit sizes of 36#, 80#, and 120#, achieving a surface roughness of Ra ≤ 1.65μm. Before polishing, the pipeline pass rate was 60–70%, which increased to over 90% after the process.
**3. Efficient Belt Grinding for Spiral Steel Pipe Welds in the West-East Gas Pipeline Project**
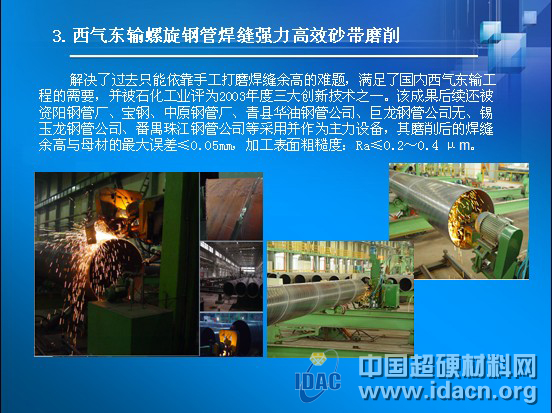
This solution replaced manual weld grinding, meeting the requirements of the domestic West-East Gas Pipeline Project. It was recognized as one of the top three innovations in the petrochemical industry in 2003. The technology has since been widely adopted by leading steel pipe manufacturers, including Ziyang Steel Pipe Plant, Baosteel, and others. It ensures a maximum seam height error of ≤0.05mm and a surface roughness of Ra ≤ 0.2–0.4μm.
**4. High-Efficiency Precision Belt Grinding for Nuclear Power Vessel Welds**
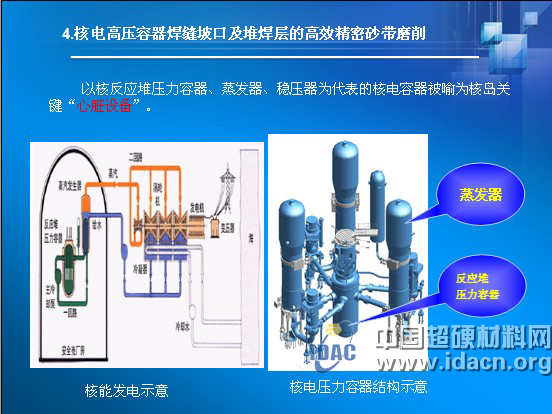
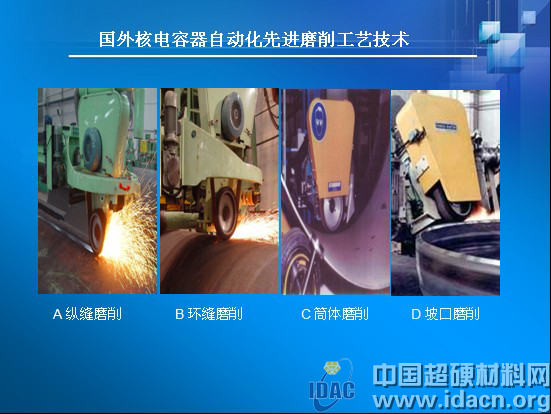
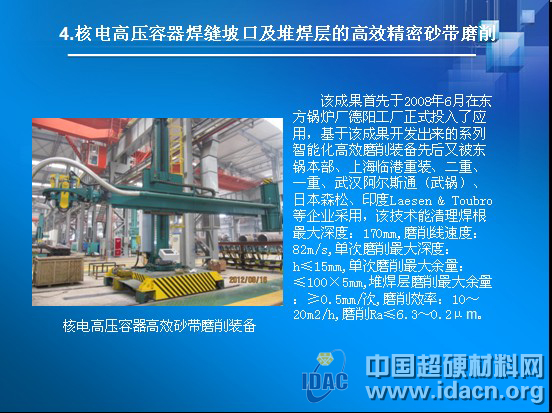
This advanced system was first deployed at the Deyang Factory of Dongyang Boiler in June 2008. The intelligent and efficient grinding equipment has since been used by companies such as Dongfang Headquarters, Shanghai Lingang, Wuhan Alstom, Japan Sensong, and India Laesen & Toubro. It can handle a maximum root cleaning depth of 170mm, with a grinding speed of 82m/s and a single grinding depth of up to 15mm. The surface roughness reaches Ra ≤ 6.3–0.2μm, offering exceptional performance in nuclear power vessel applications.
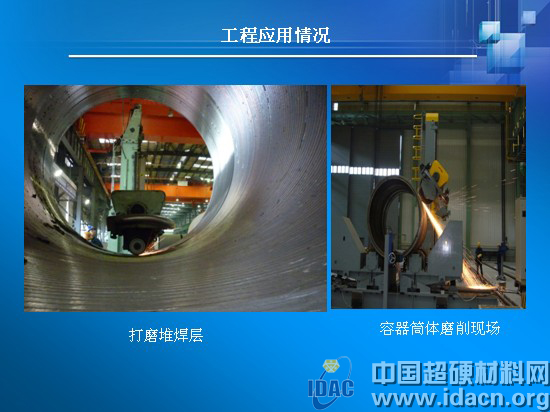
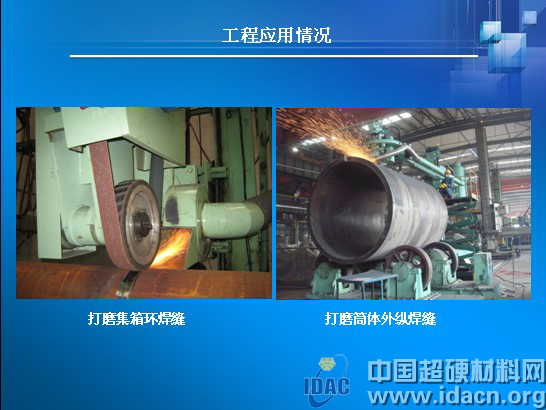
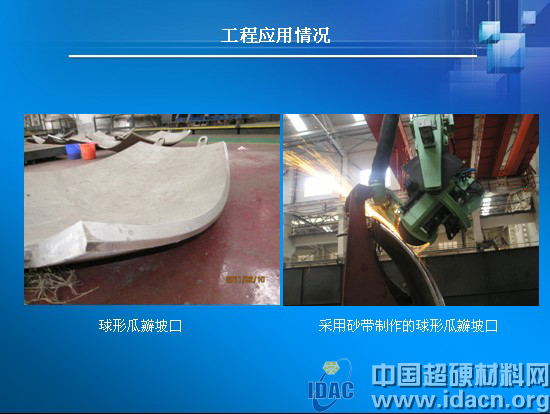
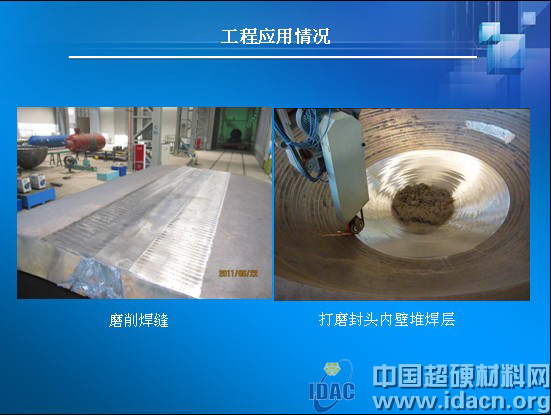
These technologies represent a significant advancement in industrial grinding, enabling higher productivity, better precision, and improved safety in complex manufacturing environments.
Stainless Steel 2.4mm Series Blind Rivets
TIANCHANG FASTENER SYSTEM CO..LTD , https://www.toprivet.com