Home>Bearing knowledge>The development and key skills of ultra-high speed grinding |
Development and key skills of ultra-high speed grinding
/*250*250 was created on 2017/12/25*/ var cpro_id = 'u3171089'; |
Under the same conditions of metal removal rate; the grinding wheel speed is improved from 80m/s to 200m/s; the life of the grinding wheel is improved by 8.5 times. When grinding at a speed of 200m/s; when it is 2.5 times higher than 80m/s The removal rate; the number of life is still doubled. 1 The development of ultra-high-speed grinding in Europe and Europe; the development of high-speed grinding skills started early. The basic research on high-speed grinding was started in the late 60s; the grinding speed of the laboratory has reached In the late period of 210-230m/s.70; CBN grinding wheel was used for high-speed grinding. Italy's Famir Company at the World Machine Tool Expo in West Germany at the West German Hanover in September 1973; exhibited RFT with a circumferential speed of 120m/s. C120/50R type grinding bearing inner ring outer groove high-speed suitable grinding machine. At the beginning of the 90s era; grinding test with a maximum speed of 350m/s has been completed. Current; practical application; high-speed grinding and fine grinding maximum grinding The cutting speed is between 200-250 m/s. Guhring Automation of Germany produced a powerful grinding machine with a power of 60 kW, a speed of 10,000 r/min and a grinding wheel diameter of 400 mm in 1983. Aheng University of Technology's super high-speed grinding machine with a guideline of 500 m/s It is also the company's production of high-speed grinding of German CBN grinding wheel; a typical For example, processing gear teeth; at a speed of 155m / s; with a resection rate of 811mm3 / mms; completed the efficient processing of 16MCr5 steel gear. Another example is: using electroplated CBN grinding wheel; at 300m / s speed With the removal rate of 140mm & sup3; /mms; completed the efficient processing of 100Cr6 high hardness (60HRC) rolling bearing steel water pump reverse wheel narrow groove. Swiss Studer company also used modified S45 cylindrical grinding machine for 280m / s Grinding test. Swiss S40 high-speed CBN grinding wheel; at 125m / s; high-speed grinding function is the most abundant; still work at 500m / s. In addition, Kapp, Schandt, Naxa Union, Song Machinery, etc. Various high-speed grinding machines have been introduced. In the United States in 1970, Bendix Company of the United States produced a 91m/s plunge-type high-speed grinding machine. 1993; the ultra-high-speed grinding machine first introduced by Edgetek Machine Company of the United States; the single-layer CBN grinding wheel; The speed reached 203m / s, used to process hardened sawtooth and so on can reach a high metal removal rate. Centerless grinding machine for grinding research and development center of Connectient University, USA; the highest grinding speed is 250m / s; Shaft power 30kW, conditioning disk rotational speed 12000r / min; active balancing wheel; active feeding.
At present, the high-efficiency grinding grinder in the United States is very popular; the first is to use CBN grinding wheel. It can complete the resection rate of 75mm3/mms at a speed of 160m/s; high-efficiency grinding of superalloy Inconel718; Ra1~2μm after processing; ±13μm. Another ceramic CBN grinding wheel with a diameter of 400mm; grinding at a speed of 150-200m/s; reaching Ra0. 8μm; scale public service ± 2. 5-5μm. An important research direction of high-speed grinding in the United States is Low-damage grinding of high-grade ceramics. The traditional method is to use multi-step grinding; while high-speed grinding attempts to use coarse finishing for one-time grinding; high-quality silicon nitride ceramic parts with high data removal rate and low cost. Japan Japan's high-speed grinding skills have been developed rapidly in the past 20 years; in 1976; CBN grinding wheels were used for high-speed grinding at 40m/s at the beginning of cam grinding machines, around 1985; on cam and crankshaft grinding machines; grinding speeds reached 80m/ s. After 1990; the development of ultra-high speed grinders above 160m/s. Currently; useful super-high speed surface grinders with a grinding speed of 200m/s.400m/s have also been announced; the maximum speed of the grinding spindle 3000r/min; maximum power 2 2kW, using a grinding wheel with a diameter of 250mm; the highest peripheral speed is 395m/s. The effect of speed on the machinability of cast iron is studied in the speed range of 30-300m/s. Toyota Machine, Mitsubishi Heavy Industries, Okamoto Machine Works, Japan The company can produce super high-speed grinding machines using CBN grinding wheels; CA32-U50A CNC super high-speed grinding machines introduced by Mitsubishi Heavy Industries of Japan; ceramic contact agent CBN grinding wheels are used; the peripheral speed reaches 200m/s. Late; 1974; the top automobile factory, the top grinding wheel factory, the Wafangdian bearing factory, the Huazhong Institute of Technology, the Zhengzhou Sanmao Institute, etc. successively carried out the grinding test of 50-60m/s; Hunan University carried out the high speed of 60-80m/s Grinding test. October 1975; Nanyang Machine Tool Plant successfully produced MS132 80m/s high-speed cylindrical grinding machine. 1976; Shanghai Bed Factory, Shanghai Grinding Wheel Factory, Zhengzhou Sanmao Institute, Huazhong Institute of Technology, Shanghai Jiaotong University, Guangzhou The high-speed grinding test group was formed by the Machine Tool Research Institute and the Wuhan Data Protection Research Institute. The 80m/s, 100m/S high-speed grinding process was tested. Together with this; the Shanghai bed factory portrayed the MBSA1332 type 80m/s half. Active high speed cylindrical grinding Grinding power reached the yield of turning and milling. In 1977, Hunan University successfully carried out 100m/s, 120m/s high-speed grinding test in the laboratory, and 2000 CNC Machine Tool Expo in China (CCMT''2000) Hunan University introduced a CNC camshaft grinding machine with a maximum line speed of 120m/s. In 1976, Northeastern University cooperated with the new top machine tool factory; developed a F1101 60m/s high-speed semi-active piston special cylindrical grinding machine. At the beginning, Northeastern University conducted a lot of high-speed grinding experiments. The YLM-1 double-sided vertical semi-active grinding production line was developed mainly by Northeastern University; the grinding speed reached 80m/s; the grinding pressure was 2500- More than 5000N.90 years; Northeastern University began the research of ultra-high-speed grinding skills; and the first research and development succeeded in China's first ultra-high-speed test grinder with a peripheral speed of 200m/s and an additional power of 55kW; the highest speed reached 250m/s. 2 The key skill of high-speed grinding is the high-speed spindle. The progress of the grinding wheel line speed is mainly to improve the rotation speed of the grinding wheel spindle. Therefore, in order to complete the high-speed cutting, the grinding wheel drive and the bearing speed are often in high demand. The high-speed spindle needs are met. Stiffness; high precision of reversal; good thermal stability; reliable; low power consumption; long lifespan, etc. to reduce the dynamic force added due to the advancement of cutting speed; the demand for grinding wheel spindle and spindle motor system is extremely accurate; and the oscillation pole small.
At present; high-speed super-high-speed machine tools produced abroad; many use electric spindles. Foreign high-speed electric spindles are developing very fast; as in Japan; at the 19th JIMTOF Expo in October 1998; the super-high-speed spindles exhibited are basically at 10,000- Between 25000r/min. The world's highest level of electric spindle is the product of Swiss Fisher Company (nmax=40000r/min, N=40kW). The high-speed electric spindle with the speed of up to 200000r/min and 250000r/min is also being developed. In the ultra-high-speed turning and milling machine developed by Shenyang Industrial College; the speed of the electric spindle is 0-18000r/min; the maximum output is 7.5kW. The GD-2 high-speed electric spindle with an additional speed of 1500r/min developed by Guangxi University of Technology Si3N4 ceramic ball bearing is used; the maximum speed can reach 18000r/min, and the main motor has an additional power of 13.5kW. The spindle bearing can be selected from ceramic rolling bearing, magnetic bearing, aerostatic bearing or liquid dynamic pressure bearing. Ceramic ball bearing has light weight. , small thermal expansion coefficient, high hardness, high temperature resistance, high temperature stability, corrosion resistance, high life expectancy, high modulus of elasticity. Its defects are difficult to make; cost is high; tensile stress The notch stress is more sensitive _ the highest surface speed of the magnetic bearing can reach 200m / s; can become a choice of ultra-high speed spindle bearings in the future. The main problem of the current magnetic bearing is the low stiffness and load capacity; the magnet used and the reverse body The scale is too large; the price is expensive. The aerostatic bearing has a high reverse tip; there is no oscillation; the conflict resistance. Mei Tuo Tuo is willing to take care of it. It is used in high speed, light load and super fine occasions. Dynamic pressure bearing; power loss is too large when no load; firstly used for low speed heavy duty spindle. Ultra high speed grinding wheel high speed grinding wheel should have good wear resistance; high dynamic balance accuracy; crack resistance; outstanding damping Characteristics; high stiffness and outstanding thermal conductivity are generally composed of a high mechanically functional matrix and a thin layer of abrasive particles. The grinding wheel substrate should prevent residual stress; the elongation during operation should be minimized. After the accounting wheel tangential and method The stress is found; the maximum stress occurs in the tangential direction of the inner diameter of the grinding wheel base; this stress should not exceed the strength limit of the grinding wheel base material. Most useful superabrasive grinding wheel bases are aluminum or steel. Japan and Europe have also developed CBN grinding wheels with other materials such as CFRP composite data. Although CFRP has a low elastic modulus, the ratio of elastic modulus to specific gravity is high; it can extend in the radial direction according to the grinding wheel. Another advantage of CFRP is lower. Linear elongation coefficient. CBN grinding wheel with CFRP as base diameter of 380mm; grinding can be completed at 200m/s; feed rate is 2m/s. Japan is on 400m/s ultra-high speed grinder; CFRP is selected as base diameter 250mm Ceramic contact agent CBN grinding wheel; grinding test of 300 m / s has been completed. Ultra-high speed grinding wheel can use corundum, silicon carbide, CBN, diamond abrasive. Contact agent can use ceramic, resin or metal to contact Jing. Resin contact agent corundum Grinding wheel with silicon carbide and cubic boron nitride abrasive; the application speed can reach 125m/s. The application speed of single-layer electroplated CBN grinding wheel can reach 250m/s, and the test has reached 340m/s. The grinding speed of ceramic contact grinding wheel can be Up to 200m/s. Compared with the grinding wheel of the base type; the ceramic contact grinding wheel is easy to dry and trim. Compared with the high-density resin and metal contact grinding wheel; the ceramic contact grinding wheel can obtain a large-scale porosity through the changing production process. The layout has a porosity of 40%. Because of the layout characteristics of the ceramic contact grinding wheel; the space of the chip after trimming is large; the sharpness is simple; even in many applications, it can be repaired. The slab-shaped sintered ceramic grinding wheel and the firm one are selected. Bonding; disposing because the coefficient of elasticity of the ceramic contact agent is too different from the matrix; and it is easy to break. The Norton Company of the United States has developed a method of manipulating abrasive particles by chemical bonding; it can make the abrasive grains 80% outstanding. The height does not fall; the tensile strength of the contact agent exceeds 1553N/mm2 (the electroplated nickel-based contact agent is 345-449N/mm2). Aheng University of Technology uses the spray skill to complete the abrasive layer on the aluminum base plate of its grinding wheel. The base is firmly bonded.
In addition, it is necessary to fully consider the reliability of the connection between the grinding wheel and the main shaft. When the main shaft rotates at a high speed, the uneven expansion of the conical joint between the grinding wheel and the main shaft occurs due to the centrifugal force; the joint rigidity decreases. The author is in the ultra-high speed grinding test; It has been presented because of the lack of clamping force; it has been in the process of launching; oscillation has occurred. Germany has announced the HSK (short-cone hollow handle) connection force and the skill of class balancing the tool and the active balance of the spindle; but it has not been used. The report on ultra-high-speed grinding. Therefore, it is necessary to develop the connection method between the grinding wheel and the main shaft with high precision, high rigidity and excellent dynamic balance function. The high-speed machining of the feed system requires not only the high spindle speed and power of the machine tool; And together with the machine tool table, there is a high feed speed and motion acceleration. The linear motor cancels the central transmission link; the so-called "zero transmission" is completed. The feed rate can reach 60-200 m/mv or more; 10-100m/s2 or more. Positioning accuracy is up to 0. 5-0. 05μm; even higher. The thrust is large; the stiffness is high; the dynamic response is fast; the stroke length is not constrained. The first problem is The heat is more severe; it has adsorption on the dust and chips around the magnetic field; the price is higher. The linear motor produced by Siemens in Germany; the maximum feed rate can reach 200m/min. The high-efficiency surface grinder developed in Japan; Linear motor; maximum speed 60m/min, maximum acceleration 10 m/s Grinding fluid and its writing system grinding appearance quality, workpiece accuracy and grinding wheel wear are largely affected by grinding heat. Although everyone developed Liquid nitrogen cooling, jet cooling, micro-smoothing and dry cutting; however, grinding fluids are still cool and smooth media that cannot be completely replaced. Grinding fluids fall into two broad categories: oil-based grinding fluids and water-based grinding fluids. (including emulsion) oil-based grinding fluid is superior to water-based grinding fluid. However, water-based grinding fluid has good cooling effect. Oil-based grinding fluid has excellent smoothing effect; it can effectively reduce chip, workpiece and grinding. The conflict between the grain cutting edge and the grinding wheel contact agent. Then reduce the occurrence of grinding heat and the wear of the grinding wheel; improve the integrity of the workpiece surface. However, oil-based grinding fluid will produce oil mist during operation; severe pollution environment; Lead to smoke and fire Unsafe; power is bad; because water-based grinding fluid has good cooling effect; good fire resistance; environmental pollution problems are easy to handle; therefore; rich in various external active agents, oily agents, extreme pressure additives, corrosion inhibitors Water-based grinding fluid with superior function of antiseptic and bactericide; it is an important development direction in these years. In addition to general grinding fluids; it can also be supplemented with gaseous or solid grinding agents. It includes mixed grinding oil and water-based composition. The combined use of grinding fluids; uniquely useful for grinding difficult-to-machine materials. Progressive smoothing with a few oil-wet wheels; water-based grinding fluids for grinding arcs to improve cooling; perhaps oil before the grinding zone; Water is only used to cool the surface of the workpiece.
After the combined use of water and oil; the appearance roughness and metal removal rate and emulsion are appropriate. Compared with the simple use of emulsion; can reduce the wear of the grinding wheel. The defect is the need for subsequent oil and water separation. High-speed grinding; airflow barrier Prevent the grinding fluid from entering the grinding zone usefully; it can also have the effect of film jubilation. Therefore; choose the appropriate injection method; it is useful to add grinding fluid into the grinding zone; improve cooling and smoothing; Improve the quality of the workpiece; reduce the wear of the grinding wheel; extremely important. Commonly used grinding fluid injection methods are: craft supply and pouring method; high pressure eruption method; air baffle assisted to cut off airflow method; grinding wheel internal cooling method; using slotted grinding wheel Method, etc. for the smooth cooling effect; generally use a variety of methods to generalize. For example; use a shoe-like nozzle; the grinding wheel can be directly smoothed in a large area in front of the wheel contact area; the nozzle itself has a flow baffle Function. The graphite tube float nozzle connects the grinding fluid with the solid grinding agent; the graphite tube itself is properly cooled in the jet of the airflow baffle; the jet and the inner cooling of the grinding wheel Tied up; impacted by radial jet; reached the effect of enhanced heat transfer; can break through the filming jubilant to hinder the joint application of high and low pressure nozzles; use high pressure nozzle and air baffle to supply liquid to the grinding wheel and grinding zone; low pressure nozzle to cool the workpiece. There is also the use of a ring nozzle to cool the workpiece; the smooth nozzle supplies liquid to the grinding wheel and the grinding zone; to reduce the overall temperature; to improve the dimensional accuracy of the workpiece. The nozzle orientation and shape have a great influence on the cooling and smoothing effect. The interval between the grinding zones; the cooling effect is reduced. Therefore, the nozzle should be as close as possible to the grinding arc zone; the useful flow and pressure of the grinding arc zone can be improved. The nozzle is optimized; the nozzle with a concave cavity is selected; Smooth; sharp edges at the exit; homogenized liquid flow; longer high-concentration jets; improved cooling and smoothing. High-speed grinding fluids need to be cleaned; filter system selection is related to chip length, thickness and type; Depending on the depth of cut of the abrasive particles. Commonly used filtration methods are: physical methods; such as gravity settling, vortex filtration, magnetic filtration, strainer filtration, filter belt (paper) filtration Chemical method; such as the use of filter aid diatomaceous earth, etc. in the filtration system through a plurality of filtration units for composite filtration; better effect. Ultra-high-speed grinding system also requires adoption to reduce the temperature of the grinding fluid; The cooling method includes natural evaporation convection heat dissipation; strong evaporation and cooling system using cooling system. In addition, the power consumption of the grinding wheel spindle caused by the grinding fluid should be dealt with; and the influence of the dynamic pressure of the grinding fluid in the grinding area on the grinding force is discussed. Optimize the supply pressure and speed for high-speed grinding. Usefully reduce power consumption and negative impact on the environment. Relevant research indicates; there is a critical speed for a certain flow rate; when the grinding wheel speed is greater than the critical speed; followed by the grinding wheel speed Adding; normal grinding force is reduced. Grinding wheel dressing is in the grinding process; the grinding wheel becomes dull; or the correct shape is lost due to wear; it is necessary to carry out timely trimming. The trimming is divided into two processes of shaping and sharpening. It is the shape and precision of the grinding wheel to reach the demand. The sharpening is to make the abrasive particles bulge the contact agent; the necessary chip space is generated; Good grinding ability. Depending on the situation; these two processes can be carried out in unison or together; can also be carried out in two steps. Commonly used shaping methods include turning, grinding, diamond roller, electric spark and laser The new plastic surgery method is also under discussion. Commonly used sharpening methods include free abrasive method (such as gas sandblasting sharpening method, free abrasive grain kneading sharpening method, hydraulic sandblasting sharpening method, etc.) and consolidation sharpening There are two major categories of things: sharpening method (such as oil stone method, corundum block cutting method, grinding wheel grinding method, etc.); in addition, electrolytic online dressing method, electric spark sharpening method, high pressure water eruption sharpening method and laser sharpening, etc. .
Regarding the new method of dressing; it should speed up the discussion of usefulness. The development of the system should give priority to the study of the general high-efficiency repair system. The research and development of the grinding and the ultra-high-speed grinding of the experimental research require a lot of manpower and material resources. The development of computer skills; the use of computers for the simulation of the grinding process is an important topic. The CIRP Grinding Technology Committee has made the "virtual laboratory" an important collaborative project; the virtual grinder can establish a realistic virtual grinding Environment; can be used to evaluate, guess the progress of grinding process and product quality, and training. It can simulate the grinding process by using computer simulation; simulate the temperature field and grinding force change in the grinding zone; analyze the grinding under different conditions. Cutting precision and grinding appearance quality. Grinding process is a multi-variable chaotic process followed by artificial intelligence skills and sensor skills; intelligent grinding has also become an important research direction. The basic intention of intelligent processing is to deal with the processing process. A lot of constant qualitative; someone has to interfere with the problem of disposal. Replaced by the computer Some of the mental work of people in the process of extending the process. The key to the decision-making, monitoring and control of the process of processing is the initiative of the resolution plan. The fundamental structure of the machine tool intelligent grinding system consists of the following two parts: Sensor integration module. Use multi-sensor information blending skills; process processing information; provide more accurate and reliable information for resolution planning and control. Multi-sensor information blending methods include weighted uniform method, Kalman filter, Bayesian estimation , statistical resolution plan theory, Shafer-Dempster based reasoning, generating rules with belief factors, ambiguous logic, neural network, etc., 2 resolution planning and control module; processing information according to the processing provided by the sensor module; making a plan for the resolution; Appropriate control methods; occurrence of control information; operation of the NC controller to the processing process; to achieve optimal control; complete the processing mission of the requirements. 3 common sense library and database; register the prior knowledge of the processing process; Prior model and known The elements of processing precision; the relationship between processing accuracy and parameters related to the addition of I. In addition, it should be able to actively learn and actively protect. Huazhong University of Science and Technology, Tsinghua University, Xi'an Jiaotong University, Nanjing University of Aeronautics and Astronautics, Tianjin University, National Defense The University of Science and Technology and Northeastern University have conducted research projects such as intelligent production skills or intelligent production systems. Huazhong University of Science and Technology and Hanjiang Machine Tool Works have collaborated on the research of threaded intelligent grinding. Northeastern University is also under the auspices of the State Education Commission. Conducting research on intelligent grinding.
Recommend to friends comments close window
Bearing related knowledge |
Fag imported bearings limit speed tumbling bearing problems and diagnosis methods one-way fine crusher bearing problems solution mine and sensational mechanical bearing talk: Y-bearing with flat head screw |
This article links to http://
Please indicate China Bearing Network http://
Previous: NSK bearing radial clearance adjustment method Next: KOYO imported bearing damage reasons and solutions
Woven Geotextile is interwoven by high tenacity PET or PP filament yarn into a dimensionally stable network.
The inherent characteristics of Polyesterhigh tensile strength and modulus,low elongation, low creep and high longterm design strength makes the good ideal for soil reinforcement application. The fabric develops excellent frictional interaction with a wide variety of soil and granular materials.
The relatively low openings of these fabrics enable them to act as efficient separators preventing the mixing of costly granular materials with finegrained soils. It has reasonably high permeability to prevent excessive buildup of porepressures due to applied loadings.
Multifilament Woven Geotextile are made of individual multifilament yarns woven together into a stable fabric structure with a superior combination of mechanical and hydraulic properties. These product series has excellent resistance to biological and chemical environments normally found in soils and are stable against short-term exposure to ultraviolet radiation.
Product Features:
- High tensile strength and modulus ,low elongation, low creep and high long-term design strength.
- Ease of Construction.
- Cost effective.
- Creep resistance.
- Consistency.
- Less differential settlement
Product Application:
- Separator and reinforcement for paved/unpaved roads.
- Area stabilization.
- Basal reinforcement of embankments on soft ground.
- Reinforced soil steep slopes.
-
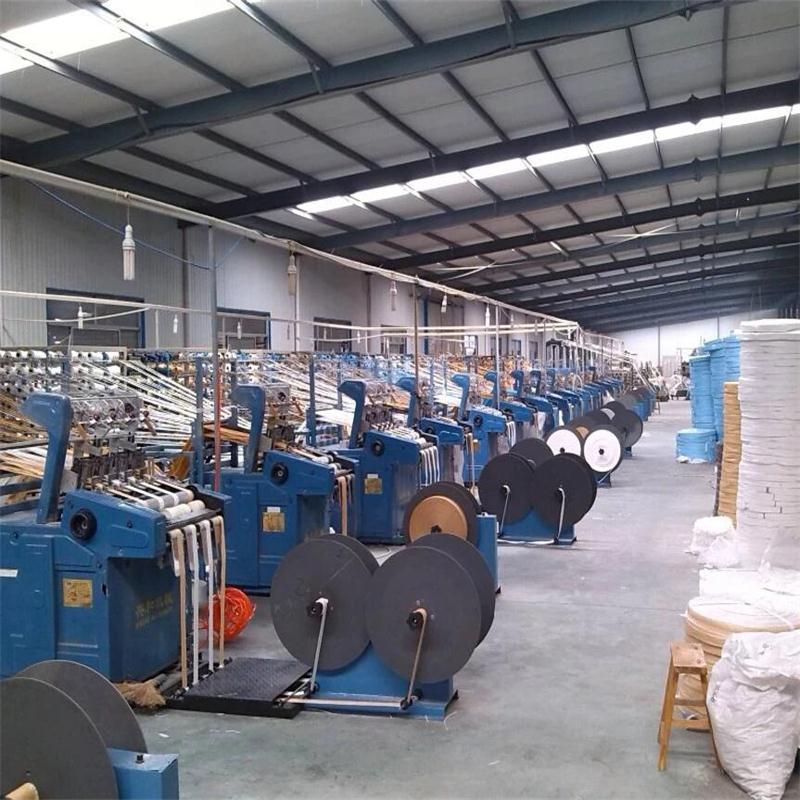
Technical data:
Pp Woven Geotextile,Polypropylene Geotextile Fiber,Pp Woven Geotextiles Geotextile,Multifunctional Woven Geotextile
Shandong Tianhai New Materials Engineering Co., Ltd , https://www.chinatinhy.com