Abstract Since 2015, the introduction of silicon wafers at the end of silicon wafers has led to a rapid decline in cost. As a result, market penetration has been rising, and the industry, which is dominated by polycrystals, has been under pressure. Compared to diamond wire cutting, it has achieved large scale in the production of monocrystalline silicon wafers...
Since 2015, the introduction of wafers at the end of silicon wafers has led to a rapid decline in cost, and the market penetration rate has been rising, which has also put pressure on the majority of companies in the polycrystalline industry. Compared with diamond wire cutting, it has already achieved large-scale application in the production of monocrystalline silicon wafers. Polycrystalline chips are still mainly based on mortar cutting. However, the application of diamond wire cutting in the field of polycrystalline has been widely discussed in the industry. At present, the main obstacle for the cutting of the diamond wire for the cutting of the polycrystalline silicon wafer is that the polycrystalline silicon wafer cut by the diamond wire has a higher reflectivity, and the conventional polycrystalline velvet process is difficult to achieve a good effect. The current mainstream technology path to solve this defect is the adoption of black silicon technology in the cell segment. If the black silicon battery achieves a large-scale mass production, the application of the diamond wire will once again pull the cost gap between the large crystal and the single crystal at the wafer end. According to a recent survey by SOLARZOOM, domestic mainstream battery manufacturers have matured their research and development of black silicon technology, and will soon be mass-produced. SOLARZOOM New Energy Think Tank believes that with the promotion of Diamond Wire Slice + Black Silicon Technology in the field of polycrystalline, the price of components will drop significantly on the basis of a 10% reduction in cost; considering the downward trend of the industry itself, it is expected that 2017 In the first half of the year, the component price including tax will fall to the range of 2.6-2.7 yuan / W. This will drive down the cost of the entire system and accelerate the arrival of the PV industry's next decade of “flat priceâ€.
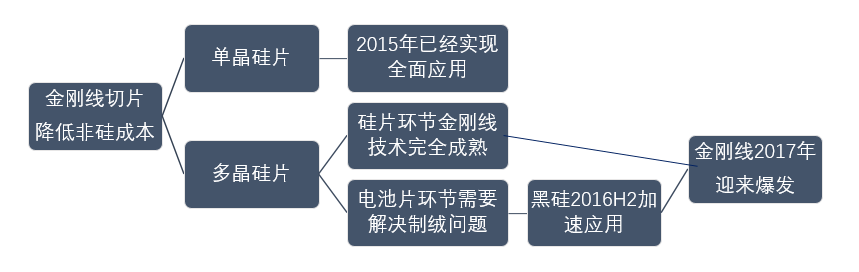
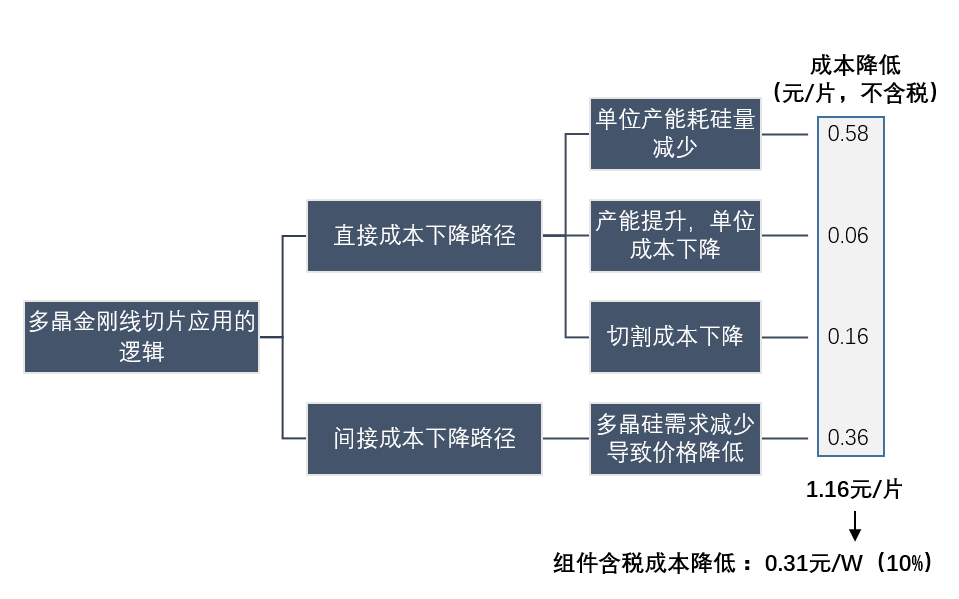
The loss of silicon material caused by mortar slicing is mainly composed of the diameter of steel wire and silicon carbide mortar. The wire diameter used for mortar cutting is generally about 110μm, and the wear of silicon carbide mortar is 60μm. The seam loss is around 170 μm. The current mainstream diameter of the diamond wire is 80μm, and the 70μm diamond wire has been used in mass production. The overall seam loss can be achieved at 90μm. Compared to the mortar section, the seam loss of the diamond wire section was reduced by 47%. According to the thickness of the silicon wafer of 180 μm and the loading of 650 mm, the number of single theoretical shots is 1767 when using mortar slicing, and the number of single shots after the diamond wire slicing is mentioned to 2287.
On the other hand, with the development of battery technology, the use of thinner silicon wafers. At present, the mainstream thickness of the silicon wafer cut by the mortar is 180 μm, and the thinnest is generally only 160 μm, which causes problems such as a drop in yield. The use of diamond wire to cut silicon wafers can now be 140μm or even lower, which can further dilute the silicon cost and depreciation of silicon wafers.
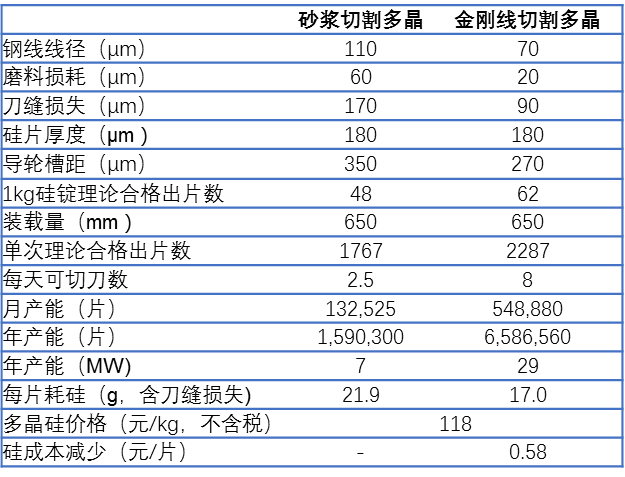
c) Reduction of cutting costs The reduction in cutting costs caused by the use of diamond wire tabs is mainly due to the reduction in the cost of auxiliary materials. The main materials of mortar slicing are steel wire, silicon carbide and PEG suspension. At present, the tax-free cost of each wafer is about 0.96 yuan. The current price is relatively stable, and there is not much room for reduction in the future. The auxiliary materials cut by the diamond wire are the diamond wire and the coolant, and the cost of the diamond wire is larger. Thanks to the rapid decline in the cost of the diamond wire in recent years, the cost of using the diamond wire cutting auxiliary materials has dropped to 0.75-085 yuan / piece. At present, the price of the electroplated wire is 0.28 yuan/m, and the price of domestic electroplating wire is about 0.25 yuan/m, while the price of the resin diamond wire used for polycrystalline chips is lower. , about 0.09 yuan / m (single piece consumption is higher, but the overall cost is still lower than the electroplated diamond wire). At present, for the wire diameter of 80μm and above, the domestic diamond wire has not been much different from the diamond wire imported from Japan. In the future, with the increase in the localization trend of the diamond line, the cutting cost of the diamond line will be further reduced.
2. The path of indirect cost reduction is significantly reduced due to the cutting loss of mortar cutting compared to mortar cutting, because the demand for polysilicon under the same capacity will be greatly reduced. If the number of qualified sheets per kg of silicon rods is increased from the current 48 sheets to 62 sheets by using diamond wire cutting, the corresponding demand for polysilicon will be reduced by 23%. If 70% of the country's polysilicon wafer production capacity is fully applied to diamond wire cutting, it will bring more than 30,000 tons of polysilicon demand per year, affecting polysilicon demand by more than 10%. In the absence of a large amount of new capacity in the downstream (in fact, there is already a serious overcapacity in the downstream), the reduction in demand for polysilicon sees the left shift of the demand curve, which causes the price of polysilicon to fall further.
In the past, this logic has been realized in the process of introducing a single crystal wire into a single crystal wire. However, since the volume of the single crystal is small, the suppression of the demand for the polycrystalline silicon material is difficult to appear. In the process of increasing the popularity of polysilicon wafer cutting, this indirect cost reduction path will accelerate, further pushing down the cost of silicon.
Black silicon technology: From the maturity to the mass production compared to single crystal silicon wafers, diamond-cut silicon wafers have encountered difficulties in the end of the battery. The consolidation cut of the diamond wire results in a shallower surface damage and a dense surface scratch on the silicon wafer after cutting, resulting in higher reflectivity. The single crystal silicon wafer is made of alkali-based velvet, and a "pyramid"-like suede structure is formed on the surface of the silicon wafer, and the shallow damage layer does not affect the formation of the pile surface. The polycrystalline silicon wafer is made of acid velvet, which has a high degree of dependence on the surface damage layer of the silicon wafer. Therefore, the diamond wafer-cut polycrystalline silicon wafer still has a high reflectivity after undergoing acid flocking, and the efficiency of the battery is higher than that of the mortar. The film is nearly 0.4 percentage points lower. This is also the most important reason hindering the promotion of diamond wire cutting technology in the field of polycrystalline.
In this context, black silicon technology has renewed its vitality. The black silicon technology adds a process after the conventional acid flocking, thereby solving the problem of excessive reflectivity of the diamond-cut polycrystalline silicon wafer, and can also be accompanied by a certain battery efficiency improvement. At present, the mature technical routes of black silicon technology mainly include dry method (RIE) and wet method (MCCE). The dry black silicon technology is better than the technology, but due to the need to add equipment and processes, the cost is changed compared to the wet technology. The current representative companies include Jingao and Jingke. The wet black silicon technology does not need to add new equipment. It only needs to make some changes and add some chemical reagents in the original equipment. Therefore, the initial investment is very small, but it also brings late investment such as environmental impact assessment. The stability is slightly inferior to the dry black. Silicon technology. The representative companies of the wet black silicon technology are Artes and Sumei's Zhonghui.
Regarding which dry and wet black silicon will become mainstream, there is no unified conclusion in the market. However, with the efforts of industry companies, black silicon technology has gradually matured. Judging from the current progress, SOLARZOOM new energy think tank has learned that some enterprises have realized small-scale mass production, which not only solves the problem of cheese-making of diamond-cut polycrystalline silicon wafers, but also achieves a battery efficiency of 0.4-0.6 percentage points. Upgrade.
New technology leads the cost reduction At present, the price of first-line polysilicon wafers will fall below 5 yuan/piece, while the price of monocrystalline silicon wafers will follow closely, down to 5.9 yuan/piece. In the ubiquitous price war and the sorrow of the industry, we faintly see the dawn of the rise of new technologies.
After the application of diamond wire cutting in the polycrystalline field begins, the supply curve of the silicon wafer will be moved down. The first to benefit is the company that originally had a cost advantage and invested in the diamond sheet of the diamond wire. They achieved a rapid decline in cost through the diamond line at the beginning, and at this time, the market price of silicon wafers has not fallen sharply due to the introduction of polycrystalline diamond wire slices, so this part of the company can obtain a certain relative income. As the diamond wire slices are gradually spread in the polycrystalline field, this part of the excess returns will gradually disappear. In the case where the cost of the single crystal does not continue to decrease, as the diamond wire is applied in the polycrystal, its position on the wafer supply curve will move to the right. In the process of gradually opening the diamond line and black silicon, some of the backward production capacity that failed to keep up with the technical trend will continue to move to the right on the supply curve until it cannot be kept up with the market demand.
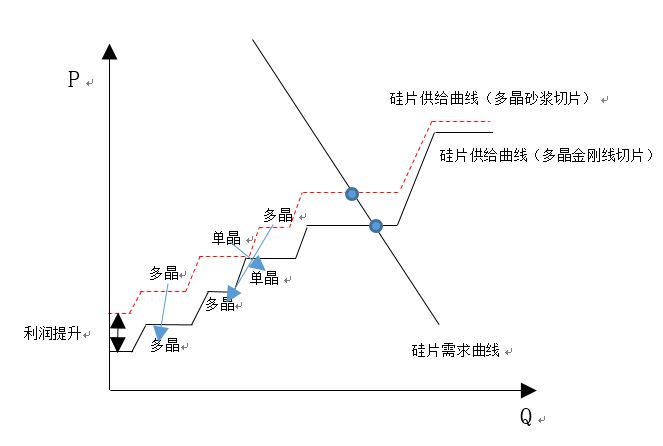
The bottom of the industry price will be further reduced. Photovoltaic ushers in the “flat price online†cycle. Currently, the price of photovoltaic products is facing a rapid decline. The price of the latest phase of the national electricity investment tendering component is 3.05 yuan/W. At present, the net interest rate of some manufacturers has begun to gradually approach zero. We judge that in the future, if the terminal demand does not fundamentally improve, the price will continue to fall, from the negative net interest rate until reaching the manufacturer's production cut-off threshold.
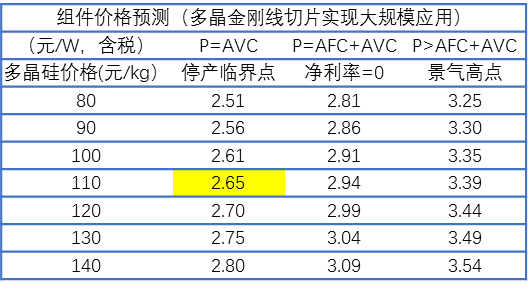
Folden Hairdryer,Motel Hair Dryers,Hotel Hair Dryer,Folden Hotel Hairdryer
Uni-Sec (Ningbo) Electronics Technology Co., Ltd. , https://www.hospitalityunisec.com